Recognizing the Key Steps in Tank Welding Inspection Procedures
Recognizing the Key Steps in Tank Welding Inspection Procedures
Blog Article
The Vital Duty of Tank Welding Assessment in Ensuring Structural Stability and Safety Compliance in Industrial Applications
In the realm of commercial applications, tank welding examination arises as an essential element in safeguarding structural honesty and ensuring compliance with safety regulations. Using a mix of strategies such as aesthetic evaluations and advanced testing techniques, these examinations offer to recognize and reduce prospective defects prior to they rise right into considerable risks.
Value of Storage Tank Welding Inspection

Guaranteeing conformity with market criteria and policies is an additional substantial aspect of container welding assessment. Governing bodies mandate rigorous guidelines for the building and maintenance of tank, and extensive examinations aid organizations follow these demands. Non-compliance can cause extreme fines, including penalties and closures, further emphasizing the demand for rigorous assessment procedures.
Furthermore, tank welding inspection plays a vital role in preserving functional performance. Regular analyses can recognize prospective concerns before they escalate, helping with prompt repair services and minimizing downtime. This positive strategy not just enhances security yet likewise contributes to cost financial savings in the long run. In recap, the value of container welding examination exists in its capacity to safeguard public health and wellness, shield the atmosphere, and ensure compliance with governing structures.
Key Inspection Methods
Efficient tank welding examination depends on a selection of vital methods that ensure thorough examination of weld high quality and structural integrity. Amongst the most common methods are aesthetic assessment, ultrasonic testing, radiographic testing, and magnetic fragment testing - Tank Welding Inspection. Each method provides special advantages in examining various facets of the weld
Aesthetic evaluation serves as the initial line of protection, permitting examiners to determine surface area issues, abnormalities, or inconsistencies in the weld bead. Ultrasonic testing utilizes high-frequency acoustic waves to find interior imperfections, such as cracks or gaps, offering an extensive analysis of weld stability. This method is specifically efficient in detecting concerns that might not be noticeable on the surface area.
Radiographic testing utilizes X-rays or gamma rays to produce photos of the welds, exposing inner discontinuities and supplying a long-term record for future recommendation. This technique is very efficient for crucial applications where the threat of failure must be lessened.
Last but not least, magnetic fragment testing is employed to determine surface area and near-surface flaws in ferromagnetic materials. By applying magnetic fields and fine iron particles, assessors can determine interruptions that may compromise the architectural integrity of the storage tank. With my latest blog post each other, these strategies form a durable structure for guaranteeing top quality welds in commercial applications.
Compliance With Security Criteria
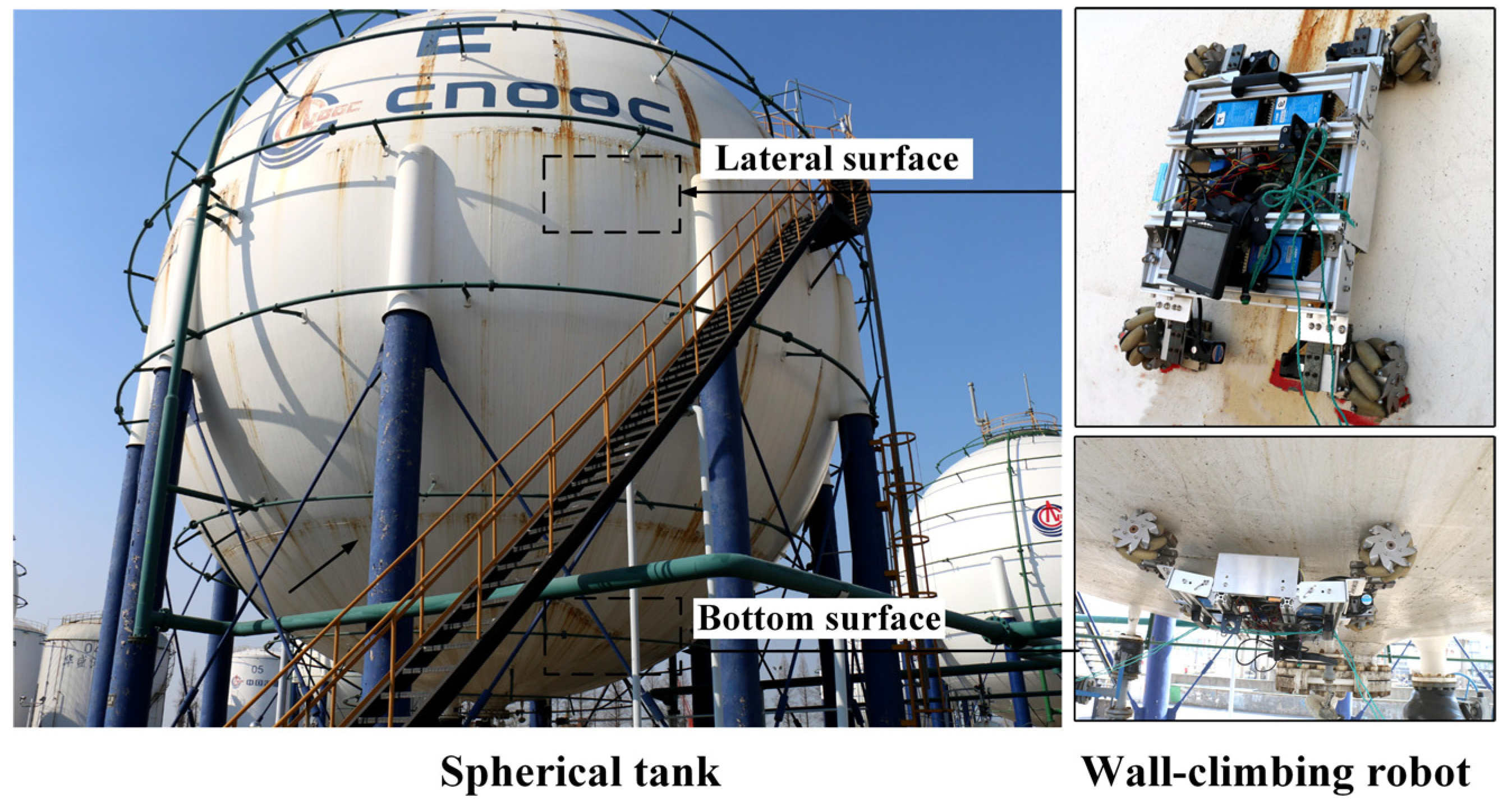
Regular assessments play a crucial duty in ensuring conformity by identifying possible failings or deviations from suggested requirements. Assessors are trained to assess weld high quality, confirm product requirements, and analyze the general structural stability of tanks. Their competence is crucial in guaranteeing that welding procedures meet the called for safety requirements.
In addition, compliance with security requirements not only safeguards workers however additionally safeguards the setting from prospective hazards such as leakages or tragic failings. Organizations that prioritize security conformity are better positioned to minimize dangers, improve functional effectiveness, and cultivate a culture of safety within their labor force. In summary, keeping rigorous compliance with security standards is vital for the effective operation of storage tank welding tasks in industrial settings.
Benefits of Regular Assessments
Normal examinations are indispensable to preserving the structural stability and safety of bonded containers. These examinations supply an organized method to determining possible issues or weak points in the welds, guaranteeing that any type of problems are addressed before they intensify right into substantial failures. By carrying out regular evaluations, companies can detect deterioration, exhaustion, and various other types of degeneration that may endanger storage tank performance.
Moreover, regular examinations add to conformity with industry guidelines and requirements. Sticking to these guidelines not just reduces legal threats but likewise boosts the organization's online reputation for safety and dependability. Normal examinations promote a proactive safety and security read review culture, urging employees to acknowledge and focus on the relevance of equipment integrity.
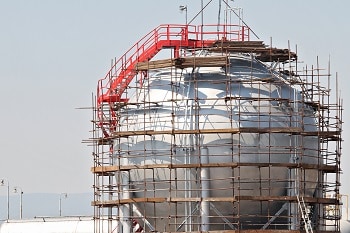
Study and Real-World Applications
Instance research studies and real-world applications illustrate the concrete effect of effective storage tank welding examination methods. Adhering to the application of strenuous welding assessment protocols, including aesthetic and ultrasonic testing, the center determined vital imperfections in weld seams that could have led to tragic failings.
Likewise, a water treatment plant executed a comprehensive evaluation program for its tank welding operations - Tank Welding Inspection. By integrating non-destructive testing techniques, the plant had the ability to detect early indicators of corrosion and exhaustion in weld joints. This timely intervention expanded the life expectancy of the containers and guaranteed compliance with safety and security policies, hence guarding public health
These situation research studies emphasize the value of regular and methodical container welding evaluations. By focusing on these methods, markets can alleviate threats, enhance structural honesty, and make certain conformity with security standards, inevitably bring about improved functional effectiveness and decreased liabilities.

Conclusion
In conclusion, container welding inspection is a vital part of keeping architectural honesty and security in industrial applications. Employing numerous assessment techniques guarantees early detection of possible defects, therefore avoiding devastating failings.
Report this page